The UMRIDA project is entering the last 6 months, and recent progress was presented in two successful dedicated sessions, as a part of the SIAM Conference on Uncertainty Quantification (UQ16), which was held in Lausanne, Switzerland begin of April 2016.
Great attention is now focused on the preparation of a UMRIDA book and Best Practice Guide on the industrial application of Uncertainty Quantification (UQ) and Robust Design Optimization (RDO) techniques. This UMRIDA book and Best Practice Guide are expected to contribute significantly to the dissemination and exploitation of UQ and RDO in industrial design practice.
Furthermore, the UMRIDA Final Symposium and Workshop on Uncertainty Quantification (UQ) and Robust Design Optimization (RDO) will take place at the premises of the Vrije Universiteit Brussel (VUB), in Brussels, Belgium on September 20-22, 2016. The following cases with prescribed uncertainties will be examined and discussed and are open to participants: NASA rotor 37, RAE 2822 airfoil, DLR F6 wing-body, Business Jet Configuration. For more information, please visit the symposium & workshop site here.
The FUCAM project (FUture Cabin for the Asian Market), which launched its activities in February 2016, performed its kick-off meeting on the AIRBUS GROUP premises in Munich, Germany, on February 25th and 26th 2016. FUCAM is a Horizon 2020 collaborative project aiming to develop a conceptual cabin interior design dedicated to the Asian markets in the year 2025 and onwards. Coordinated by Airbus Group Innovations, FUCAM brings together 8 research and industrial partners from Europe and Japan, with wide experience in their field, allowing for an unhindered course towards achieving the project’s goals.
After initiating its activities, FUCAM focused on the definition of various concept proposals and design drivers on cabin space architectures and advanced on-board systems for the Asian market. This phase started with the organization of the 1st Ideation Workshop, conducted successfully from 1st to 2nd June 2016 in Espoo, Finland. In this transcontinental joint workshop, Japanese and European partners had the unique opportunity to establish long-term trust partnerships, to participate in fruitful discussions and to share their viewpoint in the frame of identifying new concept ideas that could lead to the implementation of a future aircraft cabin dedicated to the Asian market.
Please find more information at the FUCAM website.
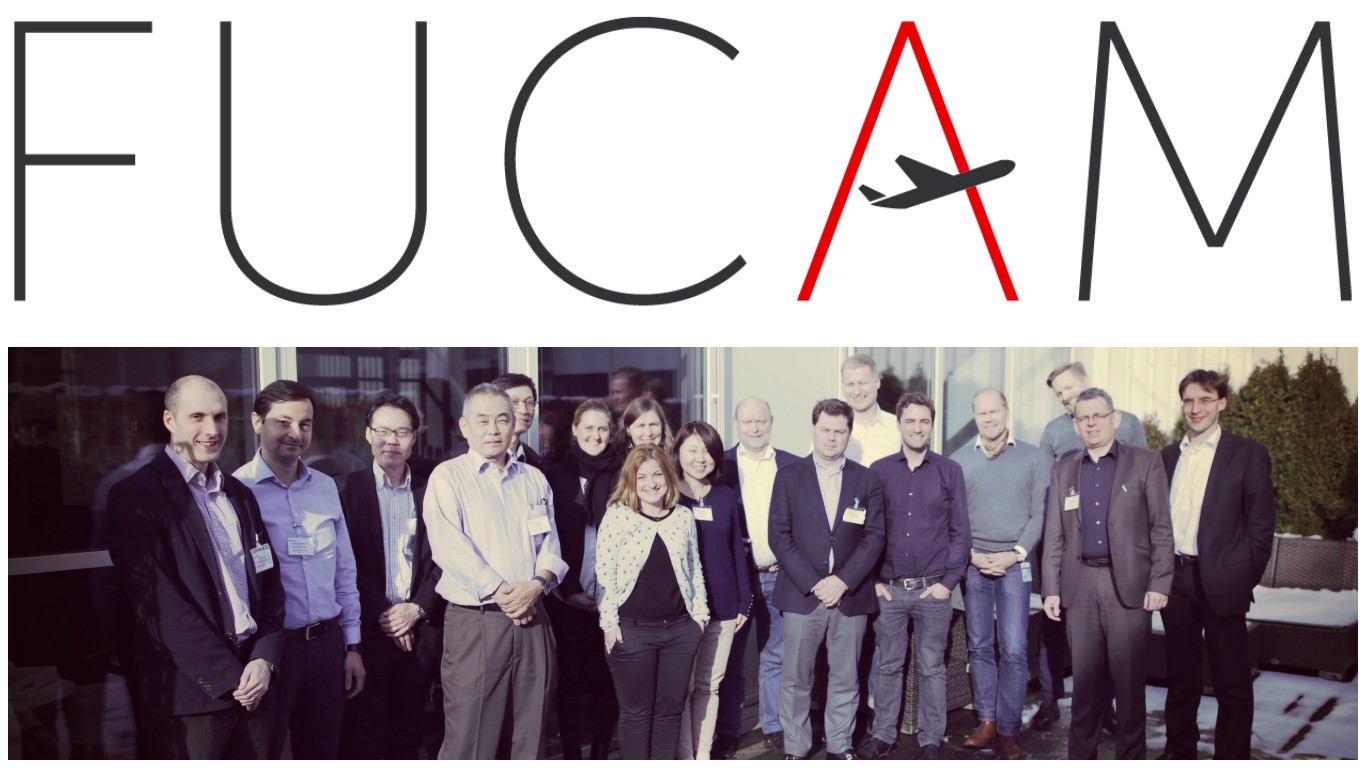
HAIC, by having achieved most of the objectives planned for its third year of activities, is moving ahead to its final 8 months of activities. The highlight of this period includes the conduction of the HAIC A340 field campaign which took place in January 2016 at Darwin (Australia) and Saint Denis (France). The main objective of this flight test programme was to validate the detection and awareness technologies developed as part of the project. The aircraft operated in both oceanic and continental convection at three flight levels (-50°C, -30°C and -10°C by order of priority).
During the campaign 34 encounters in continental convection and 46 in oceanic convection occurred. Also during this period project activities have contributed to demonstrate TRL5 maturity for a first generation of satellite-based products for aeronautic applications. In addition, detector & weather radar prototypes have been delivered to support the HAIC A340 field campaign, Ice Detection System and weather radar ice crystals awareness function standardisation activities are on-going as part of EUROCAE WG95. Finally, efforts are made to organize the HAIC Final Forum to be held at Toulouse, France between the 29th and 30th of September 2016 and prepare research actions beyond HAIC.
For more information about the latest project’s progress and achievements, please have a look at the 3rd issue of the HAIC Newsletter.

TraMOOC, being in its 2nd year of development, conducted on the 10th and 11th of May 2016 the M15 meeting in Dublin, Ireland where the progress performed during the first 15 months of the project was presented to the consortium. The aim of the M15 project meeting was to review the progress and the activities planned up to the Review Meeting in September 2016. The highlights of this period include:
- the development of the translation prototype version 1,
- the creation of the initial prototype of the automated translation functionality on iversity, connecting the iversity platform and its content with the TraMOOC translation engine, and
- the creation of the Machine Translation Version 1 (baseline phrase-based machine translation systems) which translates from English into German, Italian, European Portuguese and Greek
In a nutshell, important technical work has been performed during this period and most of this period’s objectives have been achieved. More information about the project's progress, latest results and performed dissemination activities is available on the project's progress
timeline.
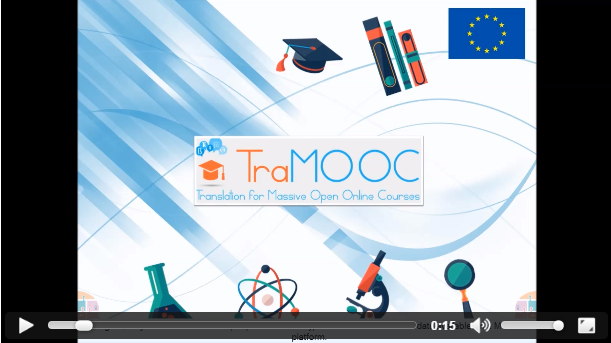
AMADE – a composite materials research group at University of Girona (Spain) – has a wide expertise on both the experimental characterization and the development of numerical methods for the simulation and design of composite materials. AMADE manages a Nadcap and ISO17025 accredited test lab that is qualified by Airbus for several advanced tests and regularly collaborates with leading companies of aerospace and automotive industries.
Find more information here.
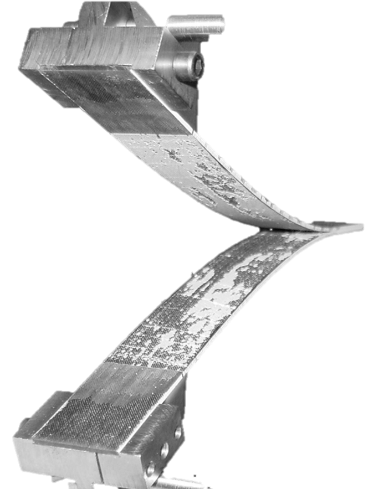
Two Clean Sky 2 proposals, NOVAIR and MANTA, that were submitted by the faculty of Aerospace Engineering, TU Delft, were successful in the second call for Core Partners for Horizon2020’s Clean Sky 2 programme. The projects received a total funding of 3.2 mE for the section Flight Performance and Propulsion, leading to a significant impulse for its scientific research programme on the development of future aircraft.
Project MANTA (MovAbles for Next generaTion Aircraft) will develop and demonstrate innovative multifunctional movables that increase airframe efficiency over the complete flight envelope of business jets and large passenger aircraft as a contribution to the societal challenge to reduce 3 to 5% CO2.
Project NOVAIR will focus on the design of radical aircraft configurations specifically exploiting the potential benefits of Hybrid Electric Propulsion (HEP). The further development of future green and sustainable air transport requires novel and radical aircraft configurations. In particular, Hybrid Electric Propulsion (HEP) is expected to have the potential to create major breakthroughs towards more electric aircraft and thus to more sustainable air transport.
Find more information here.
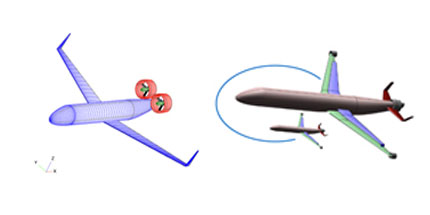
A large scale testing facility has been installed in the premises of the Laboratory of Technology & Strength of Materials of the University of Patras. The facility is consisted of 4 hydraulic actuators with maximum load capacity of 250KN and displacement range ±125mm, able to apply static and fatigue loads in three axis. The working area of the facility is 4.2m x 3.5m x 3.0m, able to accommodate and test a wide range of structures.
The hydraulic power is supplied to the actuators through a power pack system with a rate of 110 l/min at 3000psi. The facility is also equipped with a multi-channel control and data acquisition unit.
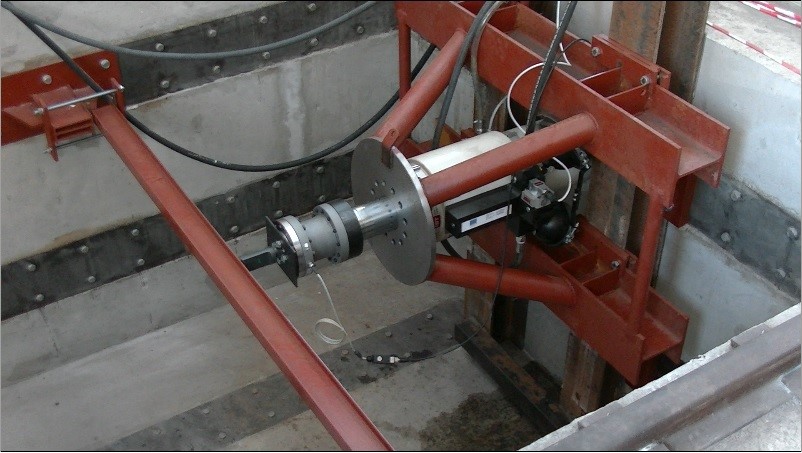
Cold spray as an additive manufacturing process —also known as 3D printing—represents a unique connection of process, materials and products which can, in the near future implemented in the aircraft industry as a repair processes for aircraft components such as rotors blades, shafts and gear boxes. In addition to being able to build new parts without welding or machining.
Impact Innovations cold spray 3D printing technology is useful in a wide range of markets, and applications and the company has already supplied the Cold Spray technology to some of the world’s largest industry innovators.
Find more information here.
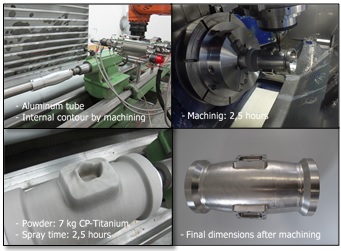
Call for collaboration at Politecnico di Milano
At Politecnico di Milano, we study cycloidal rotors in the following configurations:
- Heligyro: replacing the tail rotor of a helicopter;
- Quadricyclogyro: four-rotor aircraft;
- Cyclowing: propeller of a two-rotor aircraft;
- Cyclomobile: active spoiler for a ground vehicle.
We are currently developing
computational fluid dynamics and
multibody dynamics models with OpenFOAM and MBDyn, respectively.
Call for collaboration: anyone planning to develop cycloidal rotor models, control algorithms, experimental prototypes, or different configurations, please contact Louis Gagnon at
louis.gagnon[at]polimi.it to discuss possible partnerships.
Find more information
here.
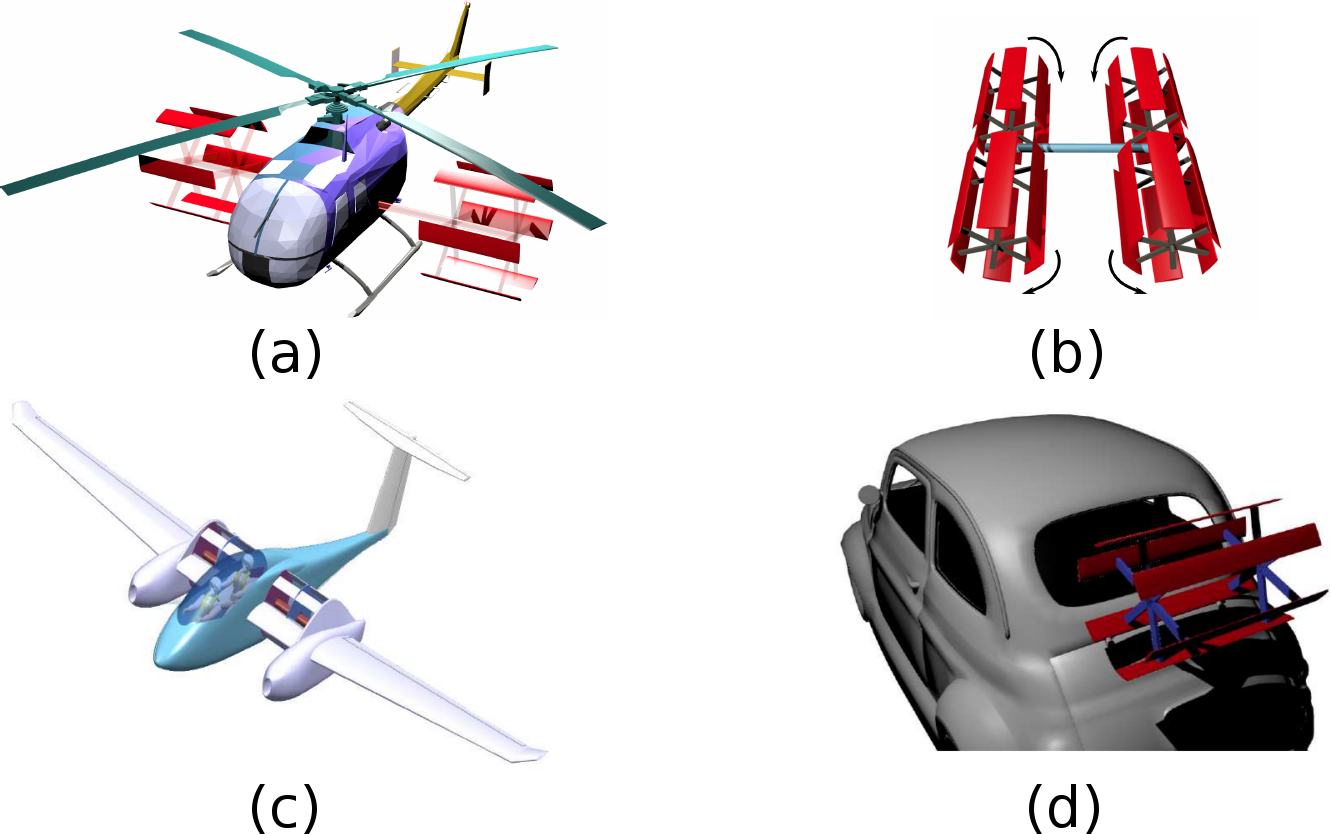
Beginning of June the Maaximus (More Affordable Aircraft through eXtended, Integrated and Mature nUmerical Sizing) project completed the manufacturing of the full scale technology demonstrator, which is going to be tested in the next months. The shell includes various innovative composite technologies for large passenger aircraft fuselages and was developed and manufactured by partners Airbus Operations, DLR and Airbus Helicopters.
Delivered to Dresden to partner IMA, the demonstrator now will be prepared for the test procedure on a novel test rig. In parallel intensive simulation work will be done to validate those numerical models, which have been developed during the first years of the project, but also to validate the structural technologies and the test stand itself. Maaximus ends 31/09/2016.
Find more information here.
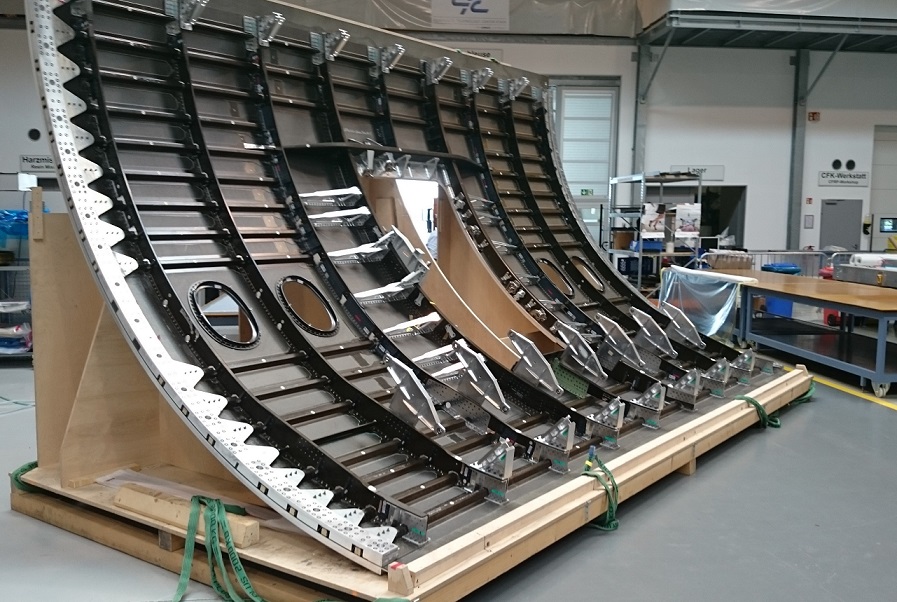
The University of Strasbourg is organising the 6th Symposium on Hybrid RANS-LES Methods in Strasbourg, France, from 26 to 28 September 2016.
The 6th Symposium provides a unique open forum for researchers and industrial engineers to exchange knowledge, to discuss new solutions of flow problems, and to present recent achievements in development and applications of hybrid RANS-LES methods - including modelling of flow physics and related numerical issues.
The 6th Symposium encourages to present new emerging ideas that may inspire future developments and applications of hybrid RANS-LES methods for improved computational accuracy and efficiency in industrial needs.
Find more information here.
LEMCOTEC: The Intermediate Pressure Compressor rig for future ultra-high OPR aero-engines was presented at Inter¬na¬tional Air Show (ILA 2016) in Berlin.
Rolls-Royce has designed a 4-stage IPC that is representative of Large Turbofan engines. The design was based around the experience of the Trent engines. Latest CFD methods calibrated to those designs were applied to introduce innovative concepts such as advanced 3D blading for transonic and subsonic stages, an integrated compressor-duct design approach and a new flow path definition. The experimental investigations have been performed at ANECOM Aerotest in Wildau in one of the largest compressor test facilities in Europe.
GKN Aerospace Sweden and the University of Loughborough are developing together an advanced compressor inter-duct. An acrylic plastic model was shown. GKN and Loughborough, with input from Rolls-Royce, designed several duct and strut configurations. The testing of lifting inter-ducts was performed at the University of Loughborough.
A new heat exchanger concept (University of Thessaloniki), air-cooled turbine nozzle guide vanes (University of Oxford), Inlet Guide Vanes (Technische Universität Braunschweig) and the ground-breaking OCORE combustion rig (DLR) were on display.
The Collaborative Project LEMCOTEC is financially supported by the European Commission within the Seventh Framework Programme. The European research project LEMCOTEC is led by Rolls-Royce Deutschland. 36 partners from aero-engine industry, universities, research establishments and small to medium size enterprises are collaborating. LEMCOTEC is developing advanced aero-engine technologies to improve the thermal cycle efficiency. Key research areas are intermediate and high pressure compressors, lean combustion and injection systems, materials and hot structures, cooling technology and combustor-turbine interaction.
Find more information here.

Development of surface pre-treatments on Ti6Al4V components to improve multi-material joining
Surface preparation is, perhaps, the most important process step governing the quality of an adhesive bond. In order to ensure the mechanical anchorage and chemical bonding of a film adhesive to a given material, the surface of the last must be clean and with a controlled macro/micro roughness. These surface properties could be achieved by different pre-treatments like laser, sanding, grinding, and in the case of lightweight alloys also by means of anodizing and plasma electrolytic oxidation (PEO) processes.
Different investigations are currently under way in CIDETEC in order develop and apply surface pre-treatments like laser, grinding and PEO processes on titanium alloys with the aim of cleaning and creating a suitable roughness and surface structure to improve multimaterial joining.
For example, in the case of laser treatments, the influence of the laser parameters (beam power, scan speed, pulse frequency, focal distance, distance and overlapping between adjacent laser traces, etc) on the topographic characteristics of Ti6Al4V surfaces are been analyzed in order to find the most suitable process parameters to improve the adhesion to CFRP.
The DAEDALOS project aimed to develop methods and procedures to determine dynamical loads by considering the effects of dynamic buckling, material damping and mechanical hysteresis during aircraft service. Advanced analysis and design principles were assessed with the scope of partly removing the uncertainty and the conservatism of today’s design and certification procedures.
The project involved 13 Partners from 8 European countries: Politecnico di Milano, Alenia Aermacchi, Aernnova, Advanced Lightweight Engineering, University of Brno, DLR, FOI, Israel Aircraft Industries, LLV, University of Hannover, RWTH, SMR and Technion.
DAEDALOS Coordinator: Prof. Chiara Bisagni, chiara.bisagni[at]polimi.it.
Find more information here.
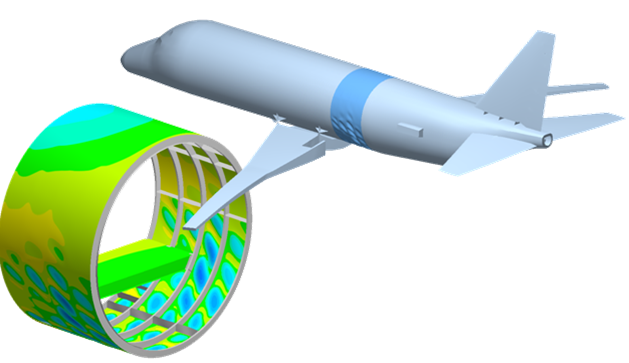
The third year confirmed good progress in all technology streams: Hybrid Laminar Flow Control on wing and fin; Active Flow Control on outer wing on wing/pylon; and on wing trailing edge; Vibrations mitigation/control in undercarriage area; Noise reduction on flap and undercarriage, but also a lot of challenges since we will have to secure the large scale testing activities such as the flight tests, wind tunnel tests and ground based demonstrators.
We organised our first workshop in September 2015 and participated in AERODAYS 2015 in October. We plan on participating to ILA, AIAA, ECCOMAS, ICAS and EASN workshop in the coming months.
Find more information here.
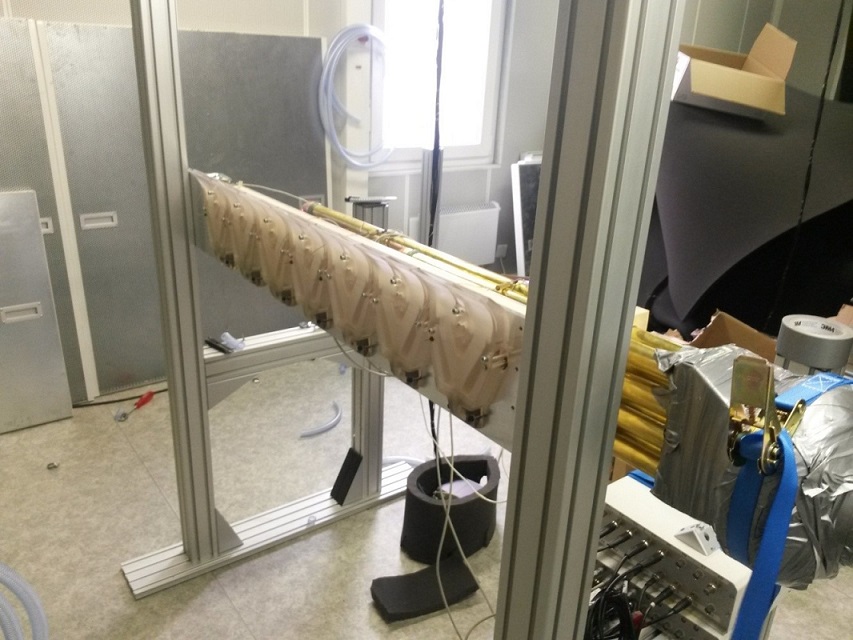
PASSME is a Horizon 2020 project focused on reducing airport travel time by 60 minutes and improving the passenger experience. Our researchers have developed a passenger-centric model which addresses the relationship between airport passengers, the airport environment, information technology and other airport stakeholders.
The project’s innovations include a personalised PASSME app, improved airport interiors, informed passenger flow management, better luggage management and a less stressful passenger experience. These are all captured in the PASSME model. This project has received funding from the European Union’s Horizon 2020 research and innovation programme under grant agreement no. 636308.
Find more information here.
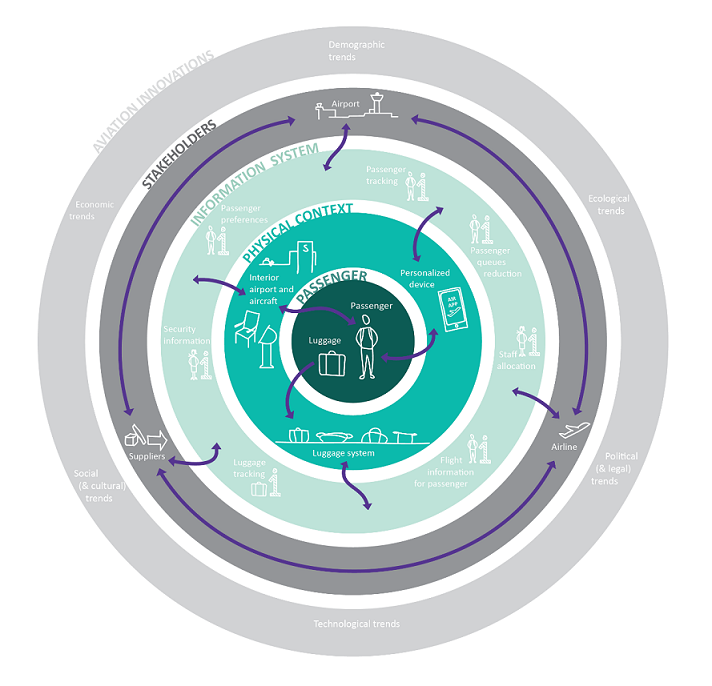
The EU technology programme ENOVAL (ENgine mOdule VALidators) has created a set of comprehensive Learning Modules. Ten modules covering different topics are available for download on the ENOVAL website. They have been designed as ready-to-teach material contributing to the transfer of knowledge between industry and academia, and facilitating the dissemination of ENOVAL technologies for Ultra-High Bypass Ratio aero engines.
All Learning Modules were realized jointly by industry and academic partners. They are equipped with valuable background information and come with a list of recommended complementary readings. They can thus be easily integrated into teaching activities at universities and other academic institutions targeting the education of future engineers in the aero-engine domain.
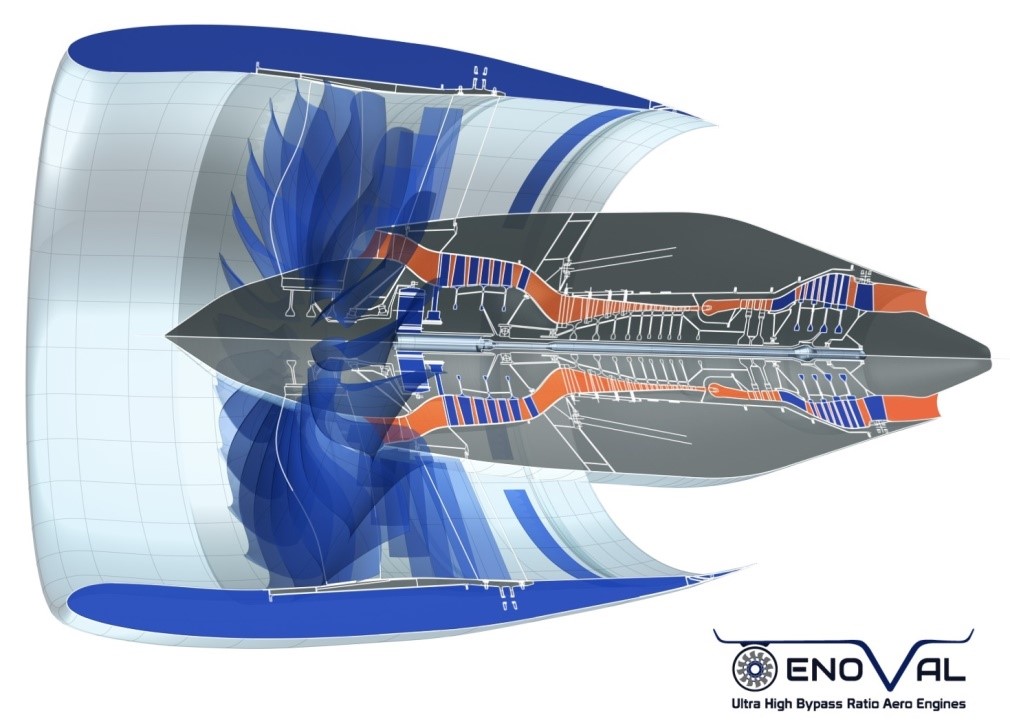
20 long haul demonstration flights on an A330-200 aircraft from KLM were successfully completed in May 2014, using the UCO-based biojet, allowing the collection of valuable in-flight data.
A series of Embraer E190 short-haul flights (Oslo-Amsterdam) have been performed, allowing further data acquisition, analysis and comparison about the performance of biojet use in different flight and aircraft types.
In January 2016, ITAKA project successfully contributed to the first commercial supply of sustainable biojet fuel through the existing hydrant system. This world’s first experience is being carried out in collaboration with Air BP and Avinor, together with KLM, SAS and the Lufthansa Group airlines (being also open to any airline departing from Oslo airport).
Find more information here.
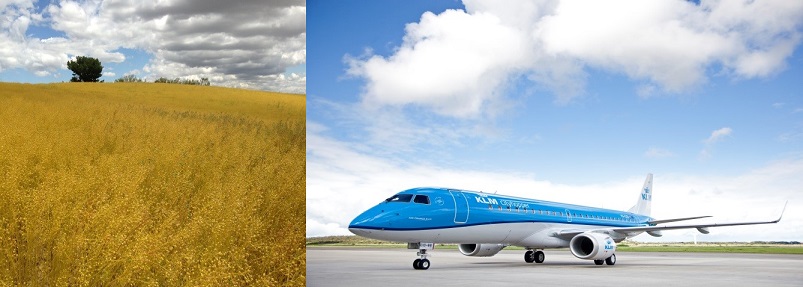